Managing Certification & Compliance for Hardware Products
Certifications and compliance regulations are not mere red tape; they serve a practical purpose in ensuring the reliability and safety of hardware products. Each certification test has a specific objective. For instance, ESD (Electrostatic Discharge) tests simulate product lifetime discharges, which is crucial for touch-enabled HMIs (Human-Machine Interfaces). Compliance with these regulations is vital for a product's functionality and performance.
To make it easier to grasp the various compliance challenges, let's break them down into five major categories:
- EMI / EMC (Electromagnetic Interference / Electromagnetic Compatibility): This category focuses on preventing devices from causing electromagnetic disturbances. Hardware companies face challenges in designing products that meet emission and immunity limits. Planning is essential, involving aspects such as circuit layout, shielding, and filtering.
- Environmental Compliance: The push for sustainability and reducing the carbon footprint requires companies to address issues like hazardous substances, recycling, and energy efficiency. Certifications such as RoHS (Restriction of Hazardous Substances) and WEEE (Waste Electrical and Electronic Equipment) demonstrate a commitment to eco-friendliness.
- Environmental Reliability: Hardware products must withstand real-world scenarios, including extreme conditions like thermal shock, water exposure, and UV radiation. The ability of a product to function effectively in such environments defines its quality and reliability.
- Safety: Safety certifications, such as CE (Conformité Européene), UL (Underwriters Laboratories), CSA (Canadian Standards Association), and BIS (Bureau of Indian Standards), ensure that hardware products do not pose any risks to users or the environment. Risk assessments, safe design practices, and comprehensive documentation are key challenges in achieving safety compliance.
- Functional Safety: Industries like automotive and medical devices cannot afford failures. Functional safety requires rigorous processes, risk assessments, safety mechanisms, and extensive documentation. Integrating these aspects into the product development cycle and fostering teamwork pose significant challenges.
EMI/EMC
Here are some of the common tests conducted under EMI/EMC (Electromagnetic Interference/Electromagnetic Compatibility):
- Radiated Emissions Test: This test measures the electromagnetic energy radiated from a product and ensures it complies with the permissible emission limits. It involves placing the product in an anechoic chamber and analyzing the radiated emissions across different frequencies.
- Conducted Emissions Test: This test evaluates the electrical noise generated by a product and conducted through its power and signal cables. It verifies compliance with emission limits and is performed using specialized equipment to measure noise levels at different frequencies.
- Radiated Immunity Test: Also known as susceptibility test, this assesses a product's resistance to electromagnetic disturbances from external sources. It involves subjecting the product to controlled electromagnetic fields and analyzing its performance and behavior under these conditions.
- Conducted Immunity Test: Similar to radiated immunity, this test examines a product's ability to withstand electromagnetic disturbances conducted through its cables and connectors. It verifies the product's resilience to interference from power lines, radio transmitters, and other potential sources.
- Electrostatic Discharge (ESD) Test: This evaluates a product's immunity to electrostatic discharges. It simulates static electricity buildup and discharges that may occur during handling or usage. The product is subjected to controlled ESD events to ensure it can withstand and operate reliably without disruptions.
- Surge Test: Surge testing assesses a product's immunity to voltage surges or transients that may occur on power lines due to lightning strikes, switching operations, or other causes. It verifies that the product can handle such electrical disturbances without damage or malfunction.
- EFT/Burst Test: This test evaluates a product's immunity to electrical fast transients (EFT) or bursts. It simulates sudden changes in voltage or current that can occur in power systems due to switching operations, load changes, or lightning. The product is subjected to these transient events to ensure its proper functionality.
- Power Frequency Magnetic Field Test: This test assesses a product's susceptibility to magnetic fields at power frequencies. It ensures that the product can operate without being unduly affected by common power frequency magnetic fields, such as those from power transmission lines or electrical equipment.
It's important to note that specific test requirements may vary depending on the industry, region, and product type. Consulting relevant standards (such as CISPR, FCC, or EN standards) and engaging with experienced testing laboratories or consultants can help determine the appropriate tests for a particular product.
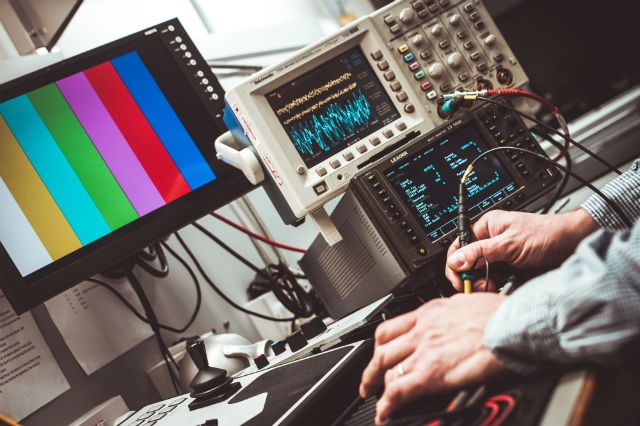
Environmental Compliance & Reliability
With increasing awareness of sustainability and environmental responsibility, complying with environmental regulations is paramount. Companies must address issues such as hazardous substances, product recycling, energy efficiency, and reducing the carbon footprint. By obtaining certifications like RoHS (Restriction of Hazardous Substances) and WEEE (Waste Electrical and Electronic Equipment), hardware product companies demonstrate their commitment to preserving the environment while ensuring the safety and well-being of end-users.
The ability of a product to function effectively in real-world environments defines its quality and reliability and following are some tests that are used to qualify the same.
- Temperature and Humidity Testing: This test assesses the product's performance and reliability under various temperature and humidity conditions. It helps determine if the hardware can withstand extreme temperatures, humidity levels, and rapid temperature changes.
- Thermal Shock Testing: This test subjects the hardware to rapid temperature fluctuations, simulating real-world conditions where products are exposed to sudden temperature changes. It evaluates the product's ability to withstand thermal stress without any adverse effects on its functionality or physical integrity.
- Vibration and Shock Testing: Vibration tests simulate the vibrations experienced during transportation, handling, or product usage. Shock tests assess the hardware's ability to withstand sudden impacts or drops. These tests verify that the product can endure mechanical stress and maintain its performance and structural integrity.
- Salt Spray and Corrosion Testing: Particularly relevant for products exposed to harsh or marine environments, this test assesses the resistance of materials, coatings, and connectors to corrosion caused by salt spray or other corrosive agents. It helps evaluate the product's longevity and durability in corrosive conditions.
- IP (Ingress Protection) Testing: IP testing determines the product's resistance to dust, solids, and water ingress. It assigns an IP rating, such as IP67 or IP68, indicating the product's ability to withstand dust particles, water immersion, and other environmental factors. IP testing is essential for products used in outdoor or rugged environments.
- UV (Ultraviolet) Testing: This test evaluates the product's resistance to UV radiation, which can cause material degradation, color fading, or performance deterioration over time. UV testing helps assess the product's long-term reliability and suitability for outdoor or sun-exposed applications.
- Altitude Testing: Altitude tests simulate high-altitude conditions to determine if the product's performance, functionality, and safety are affected at higher elevations. This is particularly important for products used in aerospace, aviation, or mountainous regions.
- Accelerated Aging Testing: This test simulates the effects of long-term usage by subjecting the product to accelerated aging conditions, such as elevated temperatures, humidity, or chemical exposure. It helps predict the product's lifespan, identify potential failures, and validate its performance over an extended period.
- Noise Emission Testing: This test measures and evaluates the noise levels generated by the product during operation. It ensures compliance with regulatory limits and helps assess the product's acoustic performance and impact on the environment and user experience.
- Chemical and Substance Testing: This test assesses the presence of hazardous substances, such as heavy metals or restricted substances, in the product. It ensures compliance with regulations such as RoHS (Restriction of Hazardous Substances) and REACH (Registration, Evaluation, Authorization, and Restriction of Chemicals), promoting product safety and environmental sustainability.
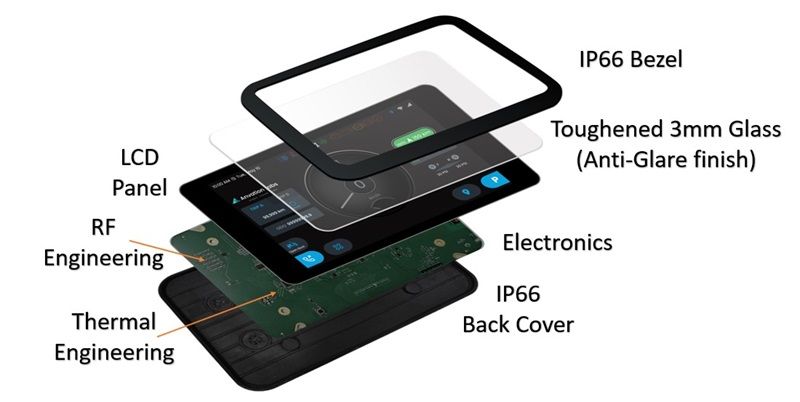
Safety Compliance
Hardware products entering the market must prioritize user safety. Compliance with safety standards (e.g., UL, CE, FCC) validates that your product meets stringent safety requirements, mitigating potential risks like electrical shock, fire hazards, and other operational hazards. These certifications instill confidence in consumers, reassure regulatory bodies, and protect your brand's reputation. Achieving safety compliance involves comprehensive risk assessments, thorough testing, and robust safety mechanisms.
Here are some of the common tests conducted as part of safety compliance for hardware products:
- Electrical Safety Testing: This test ensures that the product meets electrical safety standards by evaluating factors such as insulation resistance, dielectric voltage withstand, ground bond, and leakage current.
- Mechanical Safety Testing: It involves assessing the mechanical aspects of the product, including structural integrity, durability, and protection against hazards like sharp edges, moving parts, or potential crushing or shearing risks.
- Thermal Testing: This test evaluates the product's ability to manage heat effectively and prevent overheating or thermal hazards. It includes thermal cycling, thermal shock, and temperature rise measurements.
- Flammability Testing: This test determines the product's resistance to ignition and flame spread. It assesses characteristics such as flame resistance, fire retardancy, self-extinguishing properties, and material combustibility.
- Environmental Testing: Environmental tests assess how the product performs under different environmental conditions, such as temperature extremes, humidity, vibration, shock, and exposure to dust, water, or chemicals. These tests ensure the product's reliability and safety in real-world usage scenarios.
- Ergonomic and Human Factors Testing: This type of testing focuses on evaluating the product's usability, ergonomics, and user safety. It considers factors like accessibility, user interface design, labeling, instructions, and potential risks associated with user interaction.
- Risk Assessment and Hazard Analysis: This is a comprehensive evaluation of potential risks and hazards associated with the product's use. It involves identifying and assessing risks, determining safety measures and mitigation, and documenting risk management processes.
- Product Labeling and Marking Compliance: This involves ensuring that the product displays the necessary safety labels, warnings, and markings as required by applicable regulations or standards. It includes elements such as electrical ratings, safety symbols, product identification, and handling instructions.
- Compliance with Regulatory Standards: Safety compliance also requires adherence to specific regulatory standards and certifications applicable to the industry or region, such as UL (Underwriters Laboratories), CE (Conformité Européene), FCC (Federal Communications Commission), IEC (International Electrotechnical Commission), or CSA (Canadian Standards Association).
- Documentation and Record keeping: Maintaining comprehensive documentation throughout the safety compliance process is crucial. This includes test reports, certifications, risk assessments, user manuals, and other relevant documents that demonstrate compliance with safety standards.
Remember, the specific tests required for safety compliance may vary depending on the nature of the product, industry, and regional regulations. It's essential for hardware product companies to consult relevant safety standards and engage with accredited testing laboratories or compliance experts to ensure comprehensive safety compliance for their products.
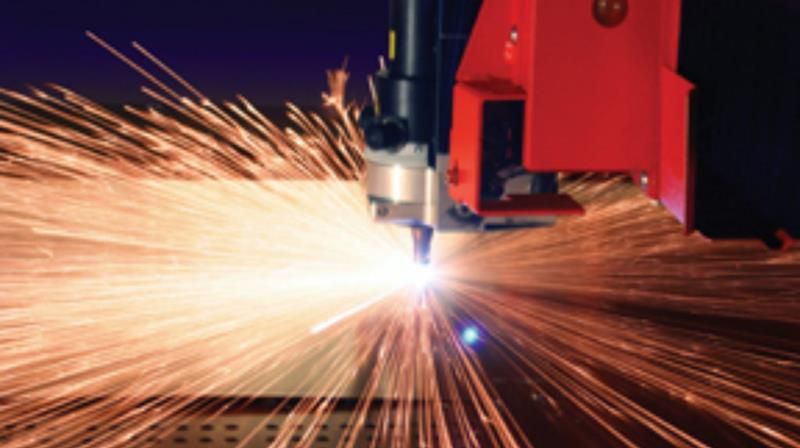
Functional Safety Compliance
In industries where failure can result in severe consequences (e.g., automotive, medical devices, industrial automation), functional safety is of utmost importance. Compliance with standards like ISO 26262 (automotive) or IEC 61508 (general) ensures that your hardware product functions safely under various conditions and takes necessary measures to prevent hazards or minimize their impact. From safety-related software to hardware redundancy, achieving functional safety compliance involves rigorous processes, thorough documentation, and comprehensive validation.
Here are some of the key tests and assessments involved in achieving functional safety compliance:
- Hazard Analysis and Risk Assessment (HARA): This process involves identifying potential hazards, analyzing their likelihood and severity, and assessing the associated risks. It helps determine the necessary safety requirements for the hardware product.
- Safety Integrity Level (SIL) Assessment: SIL assessment involves evaluating the required safety integrity level based on the potential risks and severity identified during the HARA process. It helps determine the appropriate safety measures and architectures.
- Failure Modes, Effects, and Diagnostic Analysis (FMEDA): FMEDA is conducted to assess the failure modes, their effects, and the diagnostic capabilities of safety-related components, subsystems, or the entire system. It provides critical information for determining the required diagnostic coverage and overall system reliability.
- Fault Tree Analysis (FTA): FTA is a top-down approach used to analyze and quantify the probability of system failures based on different fault events and their inter-dependencies. It helps identify critical paths and failure modes that require further attention.
- Failure Modes and Effects Analysis (FMEA): FMEA is a systematic method used to identify potential failure modes of components, subsystems, or the entire system. It assesses the effects of failures and prioritizes them based on their severity. FMEA is used to guide the design and improvement process.
- Software Safety Analysis: For hardware products that incorporate software, a comprehensive software safety analysis is conducted. This involves examining software architecture, coding standards, verification and validation procedures, and error handling mechanisms to ensure safe and reliable operation.
- Hardware Redundancy Assessment: In critical systems, redundancy is often employed to enhance safety and reliability. The assessment involves analyzing the redundancy architecture, assessing the diagnostic capabilities, and evaluating the fault tolerance of the redundant hardware components.
- Verification and Validation (V&V) Testing: V&V testing is performed to verify and validate the safety functions of the hardware product. This includes testing the product under normal and abnormal conditions, evaluating the response to faults, and confirming that the safety requirements are met.
- Functional Safety Audit: A functional safety audit is conducted to review and assess the entire functional safety process, including documentation, implementation, and adherence to safety standards. It ensures that all necessary steps have been followed and provides an independent assessment of the product's safety integrity.
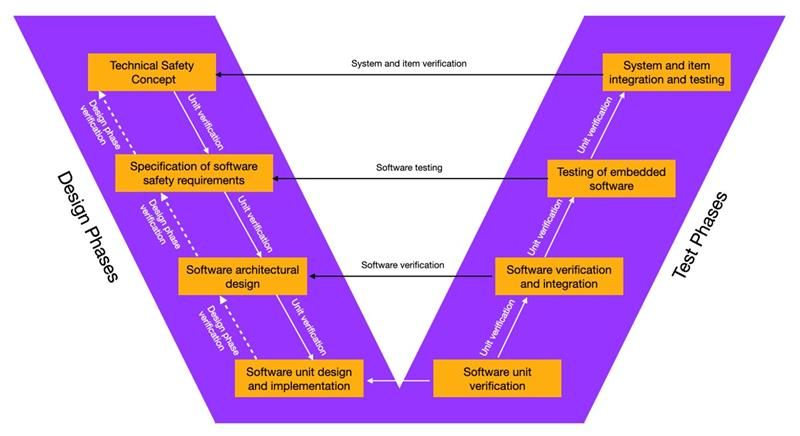
These compliance challenges are not to be taken lightly. Hardware product companies face several hurdles during their certification journey. These include keeping up with evolving regulations, managing time and resources, navigating complex testing procedures, and maintaining product innovation. However, overcoming these challenges is essential to ensure that your product meets the highest quality standards, reaches the market efficiently, and gains the trust of consumers and stakeholders alike.
Partnering with experienced compliance consultants, staying updated on regulatory changes, and integrating compliance considerations early in the product development life-cycle are key strategies to navigate the certification maze successfully.
By understanding and tackling the challenges associated with EMI/EMC, Environmental, Safety, and Functional Safety compliance, hardware product companies can pave the way for successful product launches, enhanced market competitiveness, and a safer and more sustainable future.
© 2023 Anvation Labs. All rights reserved.